Subaquatic soldering: What is isol8 doing?
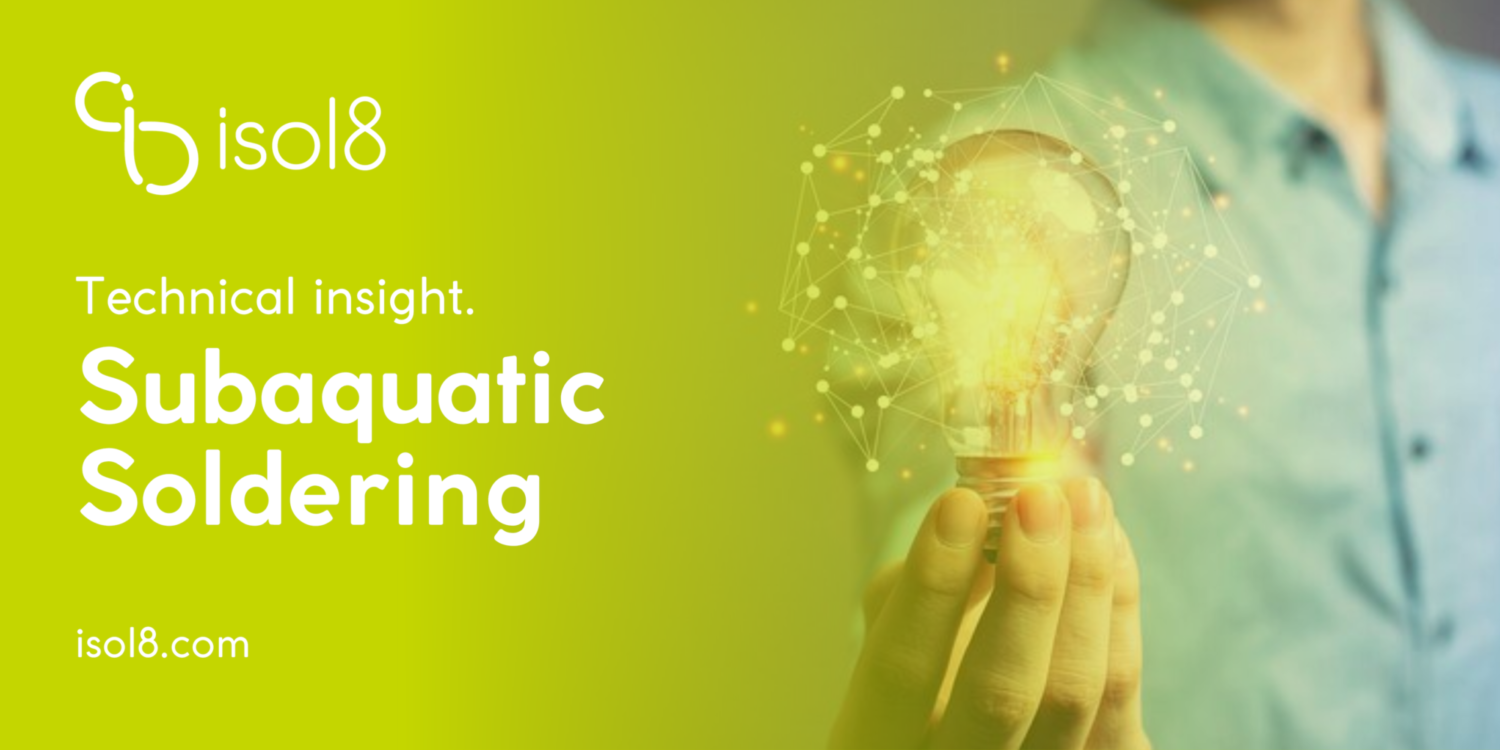
Do you know what makes isol8 unique? We are the only company in the world focused on making bonded-alloy barriers in the downhole well environment.
Our testing has shown that the best way to deliver long-term barrier integrity assurance is to bond the alloy material to the wall of the casing and/or tubing. Expansion of the alloy material alone is not enough to mitigate the creation of a micro-annulus under high differential pressures (tubing ballooning) or once the in-situ alloy stresses have relaxed.
An introduction to alloys…
To understand our technology, it’s important to understand what alloys are, and what we mean by bonded versus unbonded. Alloys are defined as metallic substances composed of two or more elements. Pure materials often have high melt temperatures and poor strength properties, so alloys are an effective way to mix different metals to make a material with the right properties.
A great example of the power of alloying is steel. It’s commonly known that carbon additions can greatly increase the strength of pure iron. Iron alone isn’t very strong, but even small amounts of carbon can make steel much harder and stronger. A lesser-known fact is how carbon can greatly lower the melt temperature to make iron easier to cast (or cast iron). Pure iron melts at 1538°C, but when 4.3% of the mass is replaced with carbon (or 4.3 wt%) the melt temperature plummets to 1147°C (something our ancestors harnessed to usher in the iron age). That’s almost a 400°C reduction in melt temperature.
Another alloying element is chromium. This can be added to pure iron to greatly enhance the corrosion properties by making stainless steel. Steel tableware can now be washed with little fear of eating iron oxide with every meal, and no longer needs to be made of precious metals like silver. These are only two different dials that metallurgists can turn. Imagine the thousands of different alloys that could be developed when you look at all 92 naturally occurring elements on the periodic table.
isol8’s range of proprietary alloy recipes have been carefully formulated, bearing in mind the melt-point, strength, corrosion resistance, wettability and aging characteristics. This is the world isol8 is submerged in when developing our low melt-point alloys – we are tailoring them to fit the most typical downhole well applications where they are required to perform.
And now let’s look at what we mean by bonded…
Put simply, we are performing underwater soldering. Soldering is most commonly used in the electronics industry where it is implemented as a joining process that rigidly attaches two or more materials together. Compared to welding or brazing (other joining processes), soldering uses alloys that melt at lower temperatures. Isol8’s bonding process forms plugs that hermetically seal up the tubing and/or casing annulus with a low melt temperature alloy (also known as solder in soldering).
The process starts by initiating a high heat-output exothermic reaction using thermite. This heats up and mobilizes our specially formulated alloys to flow where they need to form a plug. We’ll be discussing our proprietary non-dangerous goods thermite recipes in a subsequent article.
The next major step involves cleaning the tubing/casing surface with a specially formulated chemical called flux. These compounds remove the surface oxides that exist on all metals, enabling the molten alloy to create intimate contact with the bare metal. The alloy then wets and reacts with the bare metal to form intermetallic compounds, which mean a strong metallurgical bond has taken place.
These bonds are what allow our plugs to have superior performance. Our bonded alloys have delivered shear-bond strengths of 6,500psi which is greater than 20 times the shear-bond strength of cement, and greater than 10 times the shear bond strength of unbonded alloys. The intermetallic region eliminates the potential for a micro-annulus to form.
Ultimately, strong bonds are how zero emission seals can be made to last for generations.
Talk to us about how isol8 is leading the way with zero emission, highest integrity bonded-alloy barriers for every stage of the well lifecycle.
Feb 16, 2022