Fusion Annulus Casing Packers
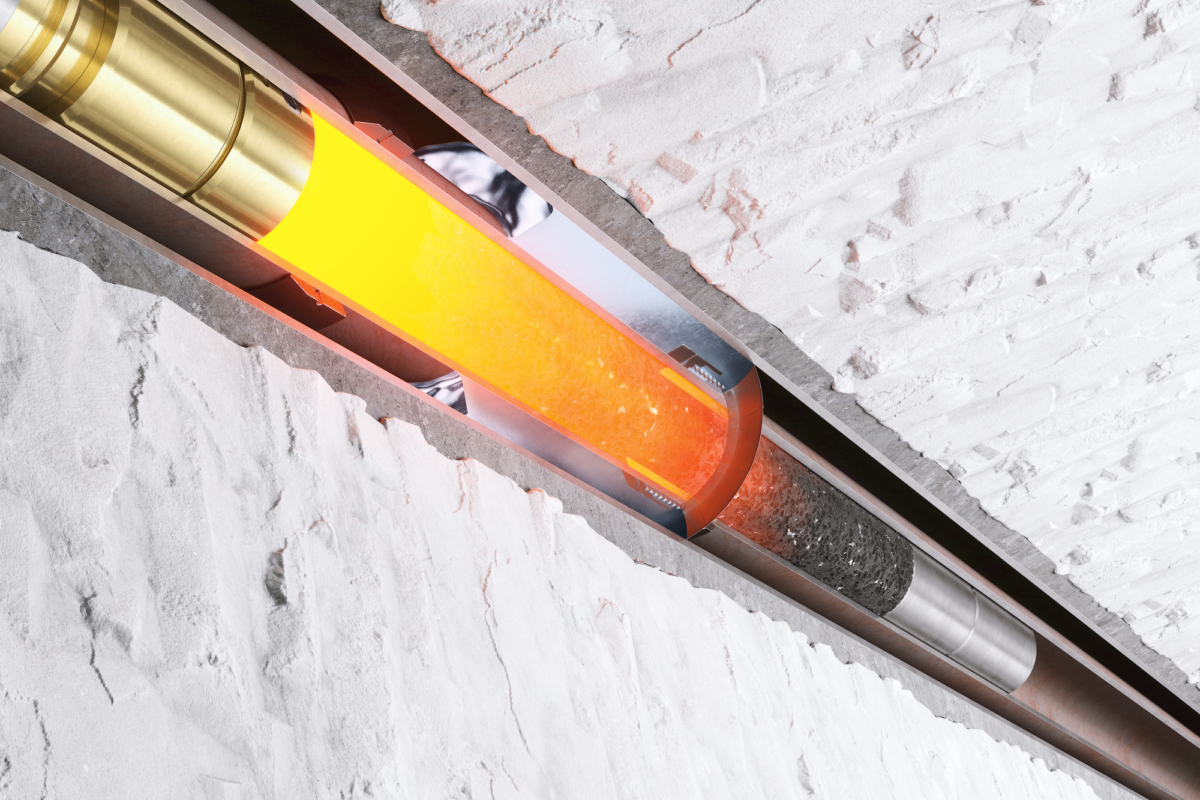
Product Applications
- A high-performance alternative to a production packer or liner hanger
- Annulus casing packer for zonal isolation
- Packer/liner hanger repair (contingency annulus casing packer can be run above a conventional packer/liner hanger)
- Remedial cement repair (the annulus casing packer can be run above the cement top to provide greater annulus seal integrity assurance)
- Well abandonment (concentric annulus casing packers placed adjacent to each other can significantly simplify well abandonment operations – ‘drill with the end in mind’)
- Gas shut off (the annulus casing packer can be run above the cement top to provide greater annulus seal integrity)
- Vent flow isolation / repair (these can be run in new wells to eliminate vent flow before it starts or can be remelted at the end of well life to establish integrity)
Product Summary
Size
The Fusion tubing packers and annulus casing packers are designed to slip over conventional joints of tubing or casing to metallurgically bond together the most common concentric string sizes.
Heater
isol8’s Fusion tubing packers and annulus casing packers are melted using retrievable thermite heaters that are deployed on wireline or slickline inside the inner string.
Alloy
isol8 is the only alloy company to create a metallurgical bond with the wellbore tubing or casing. This delivers the highest shear-bond strength and longest life expectancy. The optimum alloy is selected based on the well temperature and the alloy length can be varied to achieve the desired strength and pressure rating.
Integral Retainer
The tubing packer and annulus casing packer have been designed with an integral retainer so that our clients can be assured that there is no wasted ratty alloy run-off.
Contingency
The annulus casing packers can be run as a contingency for melting at some future date. This may be to reinstate packer integrity or to prepare the well for abandonment. They can be run above the prognosed cement top to eliminate the risk of sustained casing pressure.
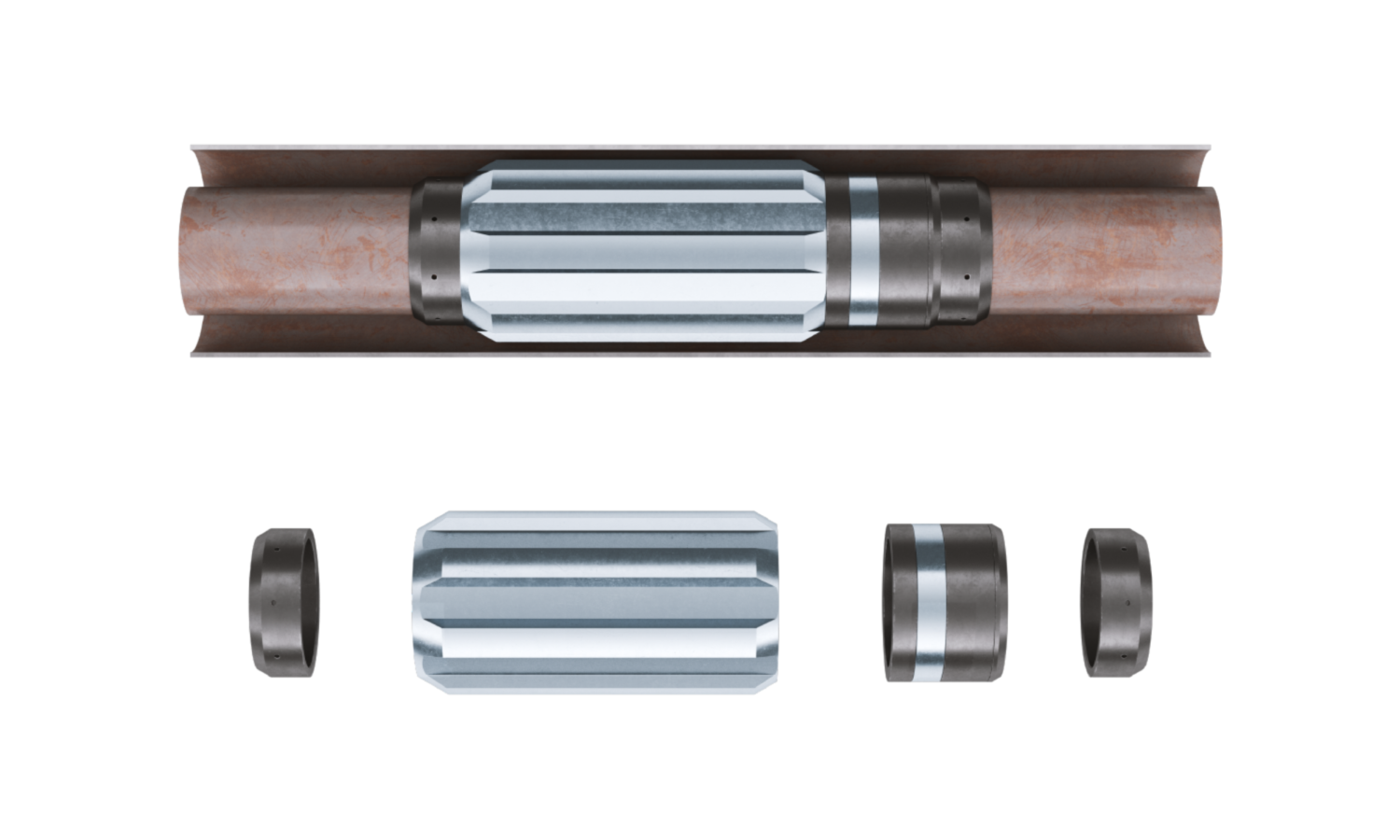
Product Features & Benefits
- Packer and annulus casing packer sizes can be customised for most tubing / casing geometries
- Slickline or electric wireline deployed heaters conveyed to the packer / centralizer depth
- Metallurgical Bond created between the concentric casings: Highest shear-bond strength and long-term integrity assurance
- Packers and annulus casing packers have an integral retainer to assure alloy barrier length
- Retainer eliminates ratty alloy run off portion in the annulus
- Placement of concentric annulus casing packers adjacent to one another can make the well “abandonment ready” and significantly reduce the asset retirement obligation
- Safe Initiation System: RP67 Compliant (Rev 3 Oct 19) Two independent safety features that prevent inadvertent tool functioning
- Secondary initiation means (100% backup – signal or timer activated)
- Thermite can provide the annular platform on which the alloy barrier can be supported
- Non-toxic alloy seal
- H2S and CO2 corrosion resistant alloy seal
- Ideally suited to CCS applications where cement degradation is accelerated by CO2
- Superior performance to cement that shrink by 1-3%
- Alloy liquid viscosity enables conformity to undefined geometries
- Alloy density displaces debris
- Alloy options to suit well temperature up to 200°C
- Barrier length can be varied to achieve the desired pressure differential to 10,000psi (or casing burst limit in certain geometries)
- Designed to exceed ISO 14310 V0 qualification standard – Eternal* gas tight seal
- Bismuth and non-bismuth alloy options are selected based on well temperature
- Thermite compacted in heaters to 10,000psi for superior heat output
* ‘Eternal’ was defined in OGUK Qualification of alternative materials for the abandonment of wells as 1 million days or 2740 Years.
Some product sizes are under development
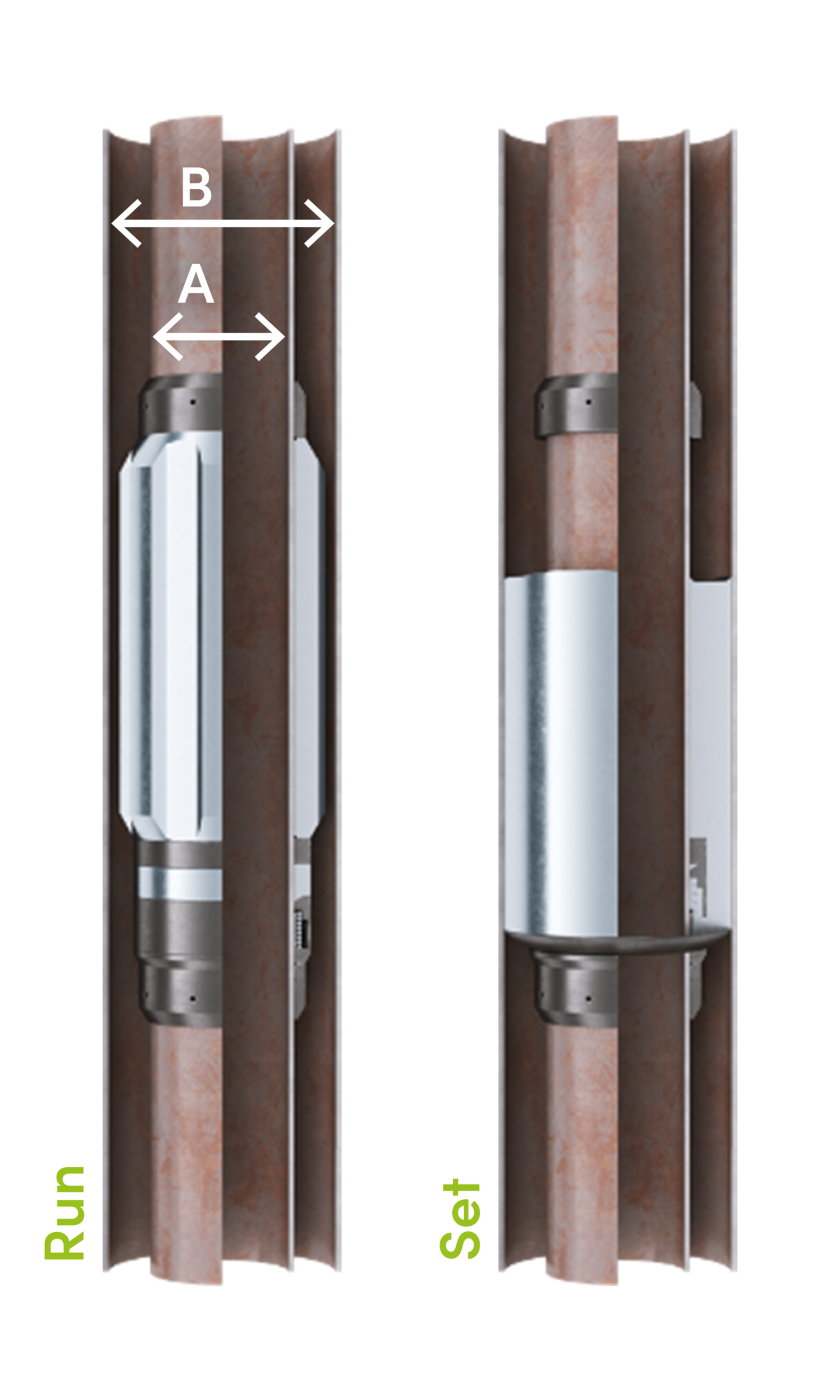
Running Tool OD | Heater OD (Solid Heater) | Tubing Size (A) | Casing Size (B) |
---|---|---|---|
3.5 | 3.5 | 4-½ | 7 |
3.5 | 3.5 | 4-½ | 9-⅝ |
3.5 | 3.5 | 5-½ | 9-⅝ |
3.5 | 5 | 7 | 9-⅝ |
3.5 | 5 | 7 | 10-¾ |
3.5 | 8 | 9-⅝ | 13-⅜ |
3.5 | 8 | 10-¾ | 13-⅜ |
3.5 | 12 | 13-⅜ | 20 |
3.5 | 18 | 20 | 30 |