Technology
The most technically advanced, metallurgically bonded-alloy barriers on the market.
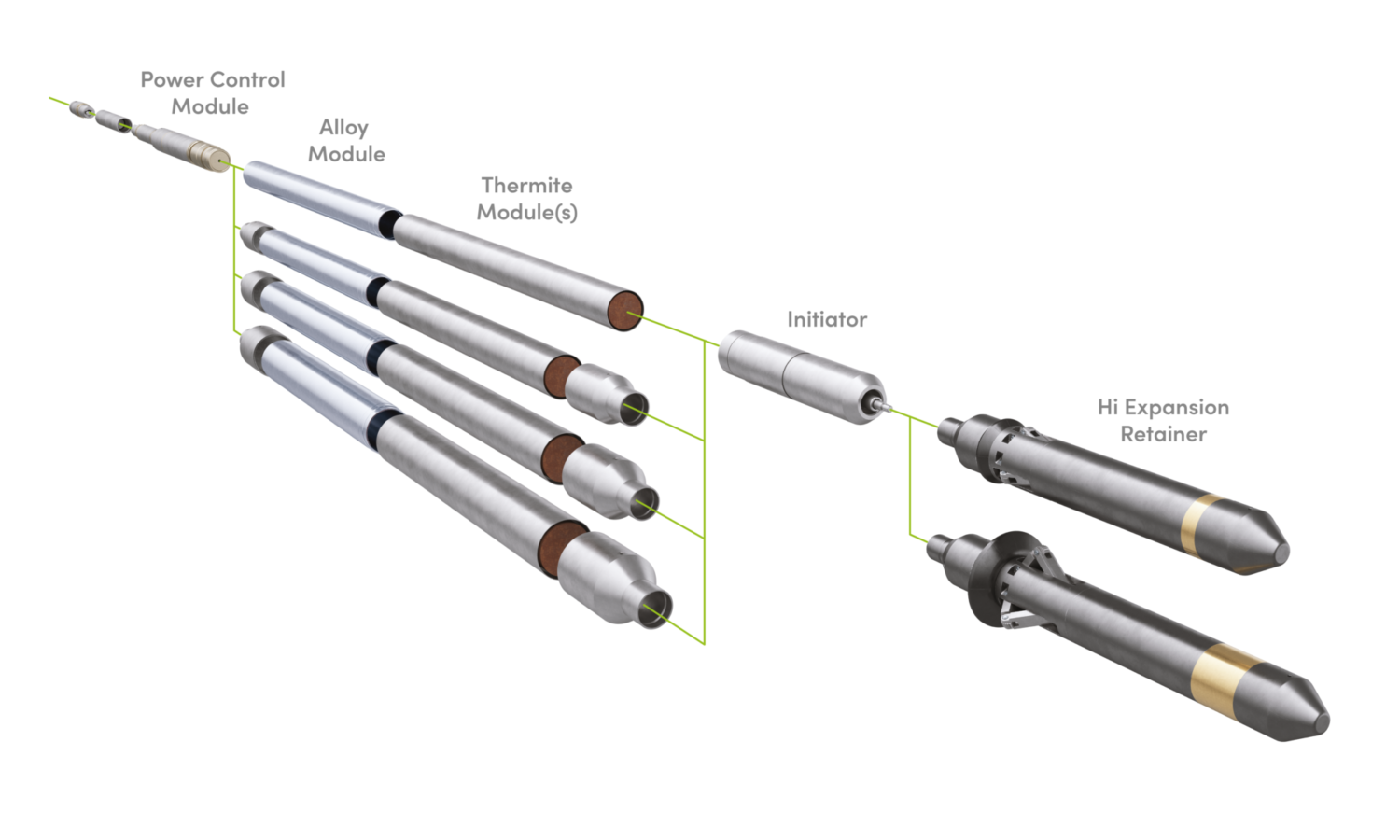
isol8’s range of Fusion products are the most technically advanced, metallurgically bonded-alloy barriers on the market. They represent a step change in downhole sealing performance with the highest shear-bond strength, greatest radial expansion capability and longest life-expectancy.
isol8’s Fusion products are designed by well engineers for well engineers.
They can be deployed on slickline, electric wireline, coiled tubing or pipe. The single trip design has an integral retainer to deliver the highest level of barrier assurance and eliminates ratty alloy.
Safety first. isol8’s initiation system incorporates 2 independent means to prevent the inadvertent initiation of the exothermic reaction at the wellsite: complying with API RP-67 (Ed 3, Oct.’19). The toolstring also incorporates 2 independently powered initiation triggers to avoid any potentially costly misrun.
Engineered for Safety, Integrity, Strength, Quality and Reliability.
Overview and Basics
isol8's alloy barriers are formed by melting alloy with exothermic heat to form a seal at the desired setting depth.
Thermite
isol8 utilises a range of different proprietary engineered thermite recipes to provide exothermic heat downhole.
The thermite can be deployed and recovered in solid form or the thermite can flow to fill the wellbore (and annulus) to generate greater radial heat when required.
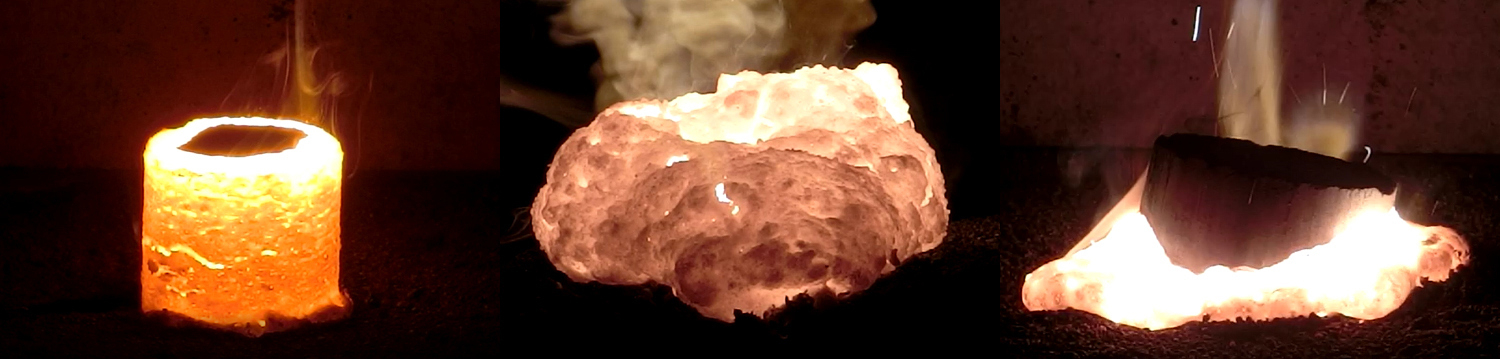
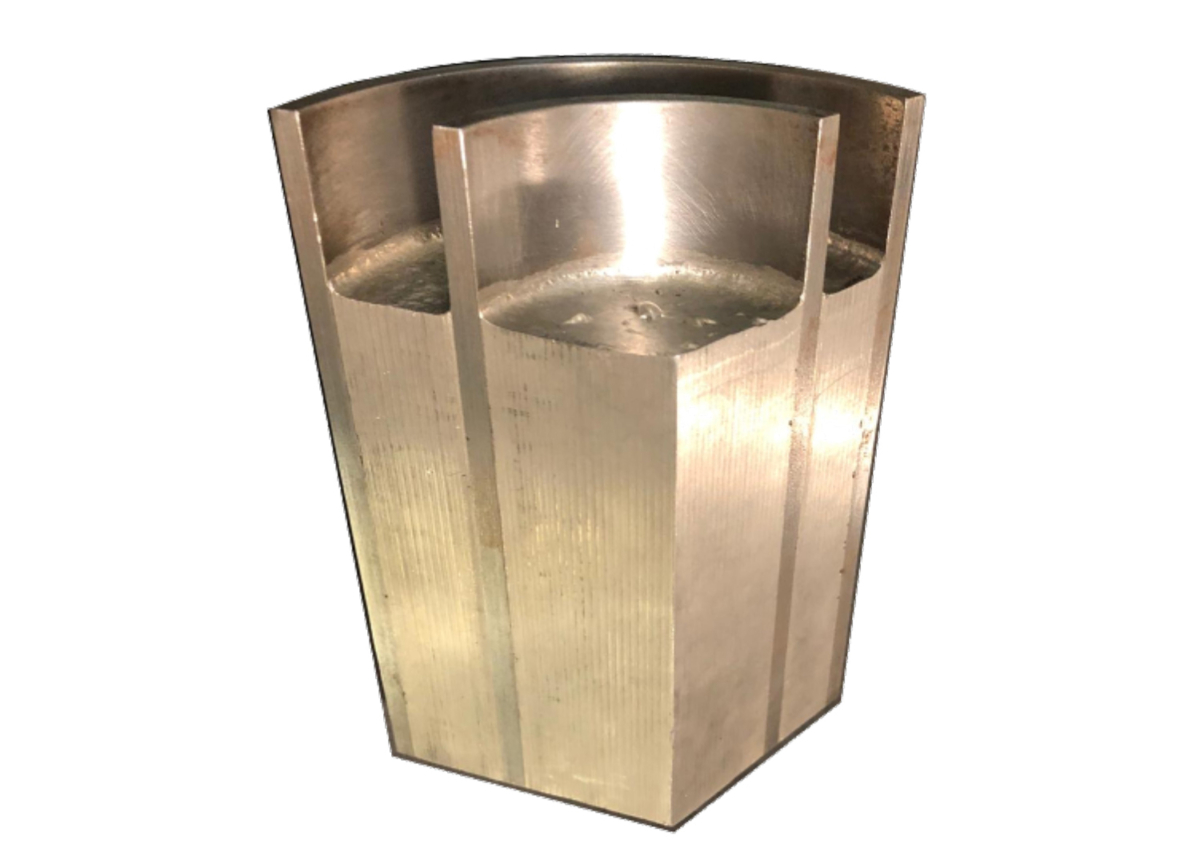
Alloy
isol8 uniquely creates a metallurgical bond between the alloy barrier and the steel tubing/casing. This provide >5 times the shear bond strength compared with unbonded bismuth alloys.
Bismuth based alloys with concentrations greater that 55% expand when cooled. These can be used to fill gaps and expand against cement or wellbore rock.
isol8 also utilises a range of other non-bismuth alloys to bond with the steel tubing/casing.
Barrier Choice Considerations
Plug expansion Ratio (Running OD vs Setting ID)
The larger the barrier expansion ratio the greater the amount of energy (heat) required to keep the alloy molten at the outer boundary.
Solid-style thermite heaters are effective for low expansion ratios.
Fluidising the thermite to flow to fill the wellbore and flow through perforations is required for higher expansion ratios.
Wellbore Temperature
The higher the well temperature the higher the alloy melt-point (and vice-versa). The wellbore temperature determines the optimum alloy choice.
Pressure Rating (Differential)
The greater the pressure differential required the longer the alloy plug length required (l/d length/diameter).
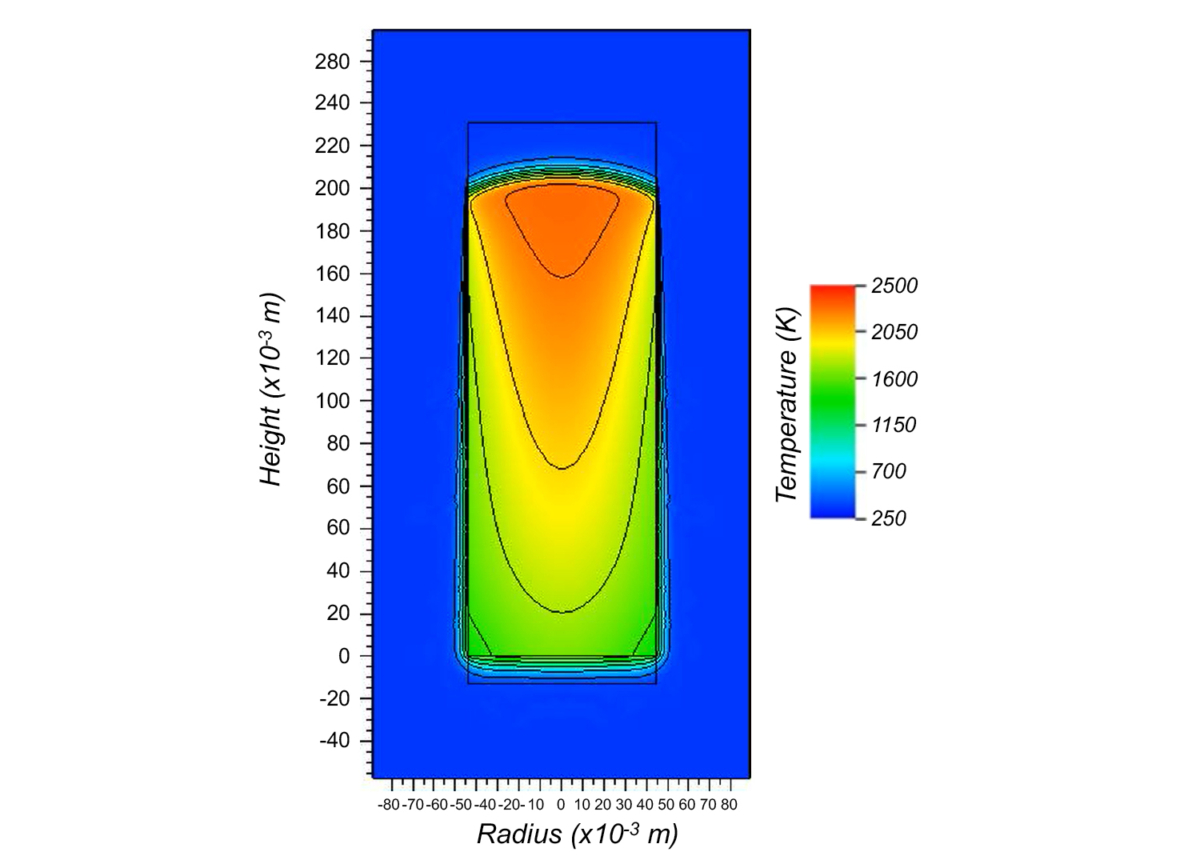
Reaction Kinetic Modelling
Determining the peak temperature, viscosity, reaction rate (cm/sec) and the solidification temperature.
isol8 has characterised >35 different graded thermite recipes. Our toolstrings typically have 4 different recipes: each performing a different function.
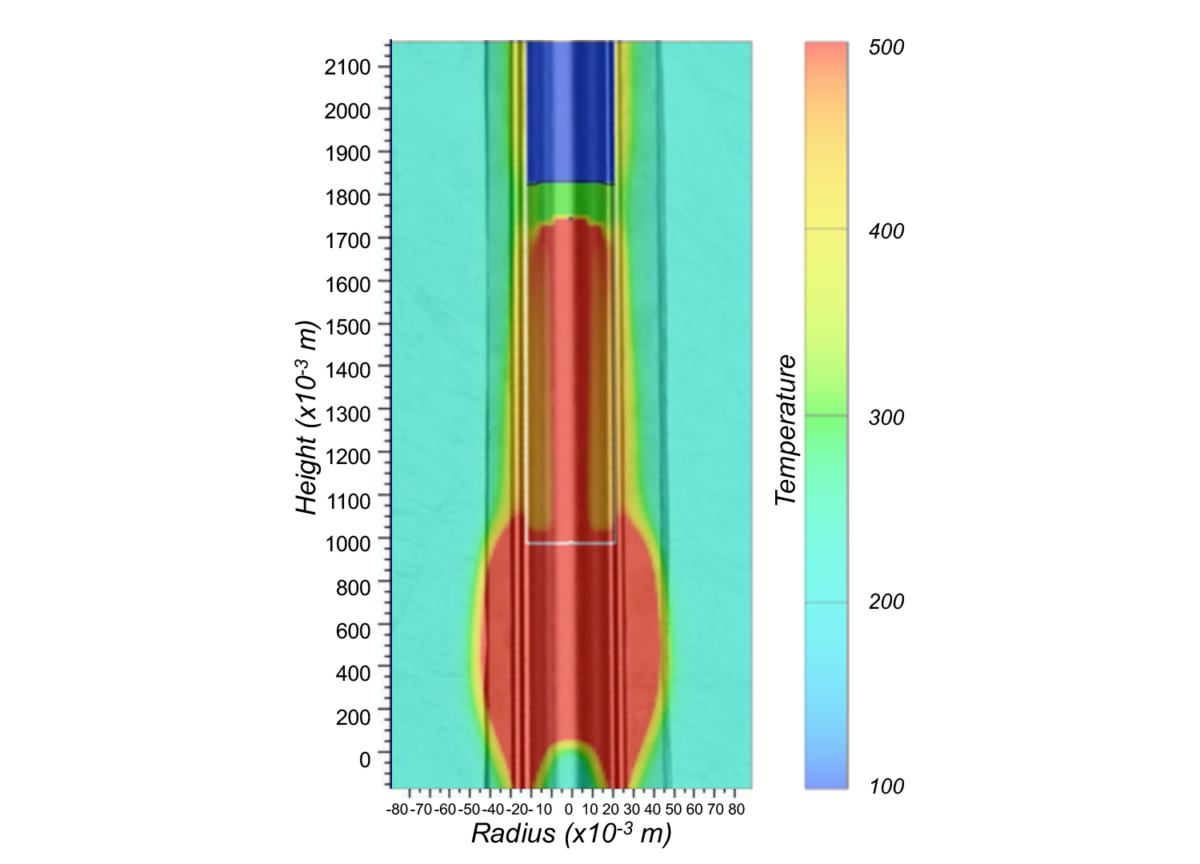
Multi-Physics / Computational Fluid Dynamic (CFD) Modelling
By inputting the chosen graded thermite product isol8 can determine the volume of alloy that can be melted in any given well geometry.

Finite Element Analysis (FEA)
isol8 performs FEA analysis on the alloy barrier in different wellbore geometries to determine the safe operating limits of the barrier.
Safety
An exothermic thermite reaction can generate temperatures approaching 3000degC.
isol8's deployment toolstring is API RP-67 compliant, incorporating a pressure/temperature module to ensure safe initiation of the thermite reaction.
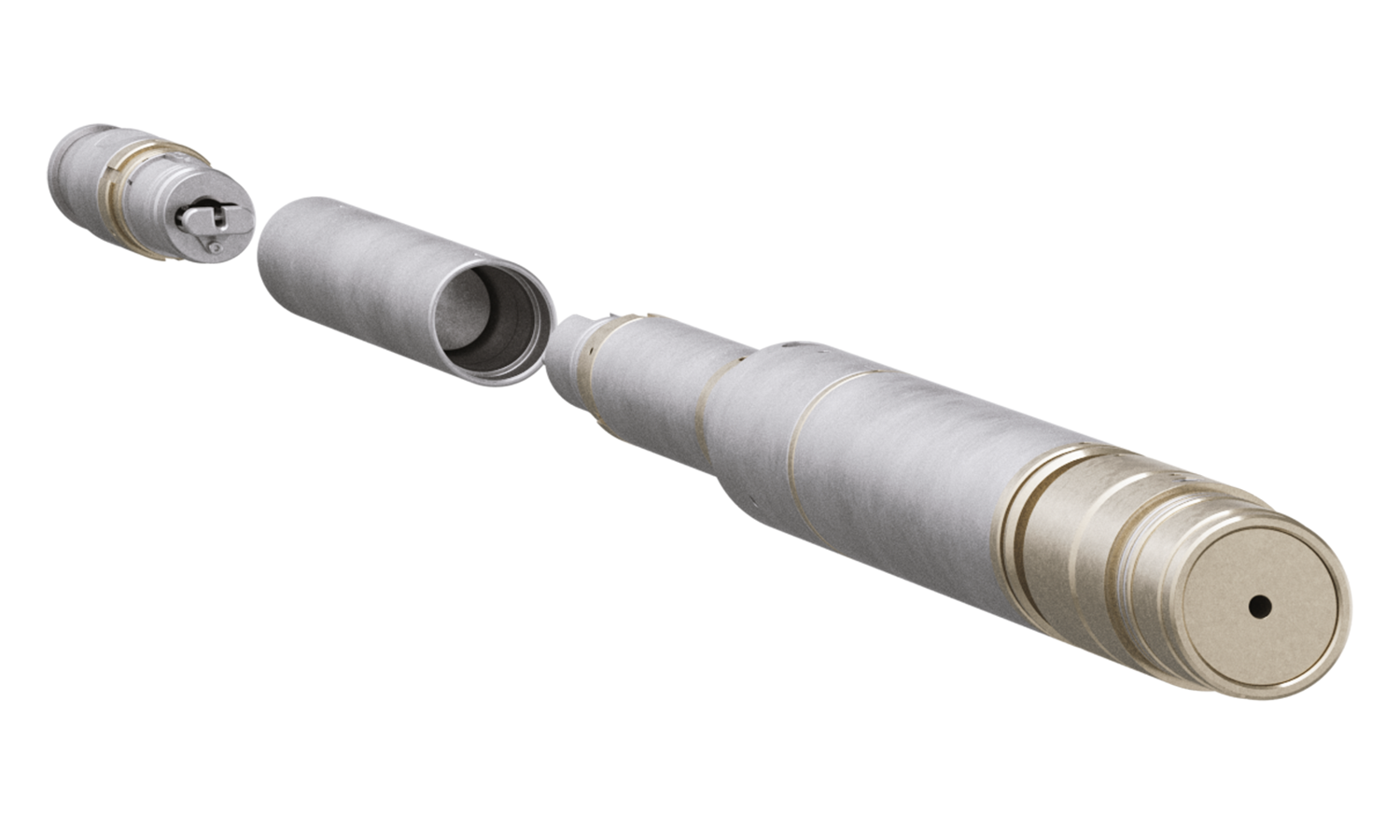
Inhouse Qualification Testing
isol8 has invested in a full-scale test vessel in which we form, test and qualify the barriers at simulated downhole pressures, temperatures and wellbore deviations.
Material testing
- Temperature, pressure, strain
- Reaction temperature, rate
- Optical pyrometry (reaction and solidification temps)
- Permeability (API RP40)
- Thermal and pressure calorimetry
- Polarizing microscopy
- Microstructural analysis: XRD, SEM/EDS, DSC, particle size, kinetics
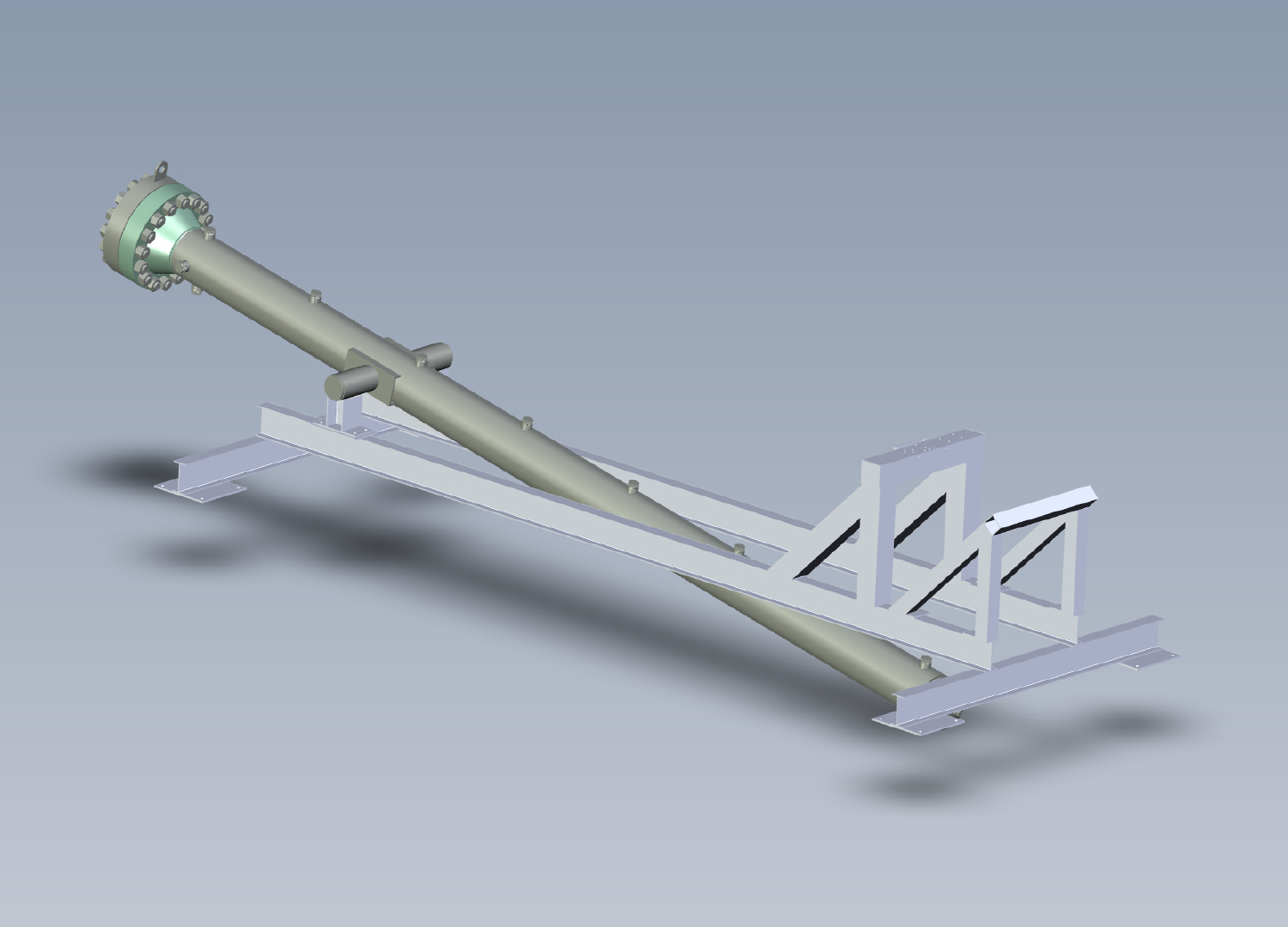